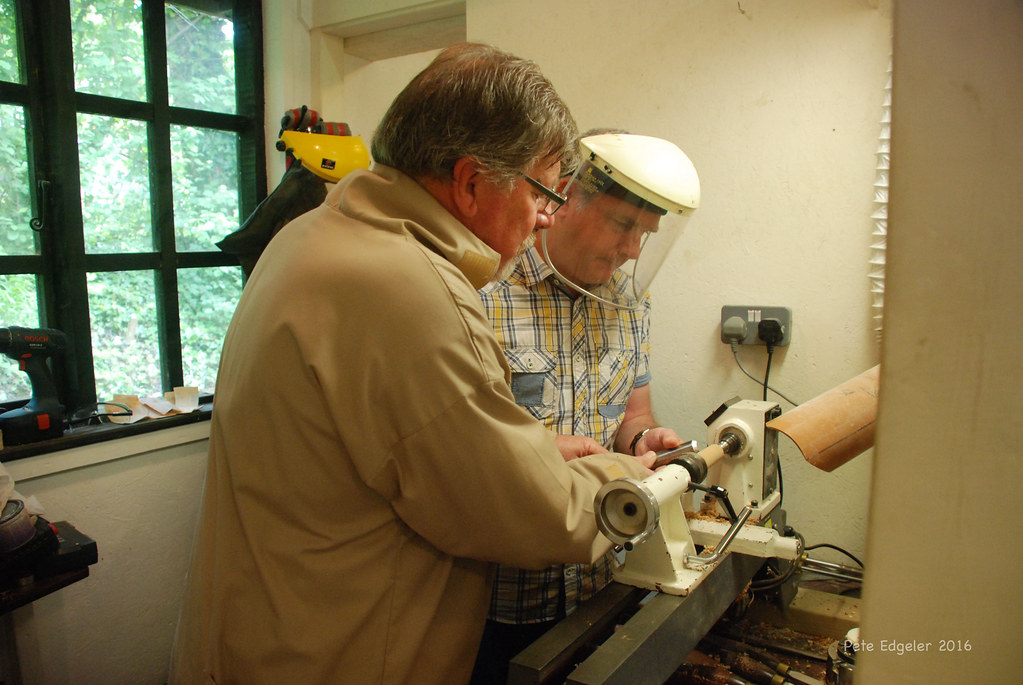
The fundamentals of segmented wood turnings are covered in this comprehensive book, which also features examples by some of the world's best turners. Keeling also covers the evolution of segmented wood turning technology, as well safety and health concerns when working with wood. There are 10 projects in the book, each with varying levels of difficulty. Also included is a gallery showing some inspiring segments. The book is intended to help beginners learn about segmented turnings but it is not meant to be an exhaustive resource for those who want to make the most beautiful turniments.
Techniques
In Techniques for Segmented Wood Turnings, William Smith provides step-by-step instructions for making segmented turned objects. This woodworking method can produce complex vessels with intricate details. This technique is particularly well-suited for beginners. Before beginning, you should have some basic knowledge of woodworking. You should also have experience in turning. Once you master the basics, you can progress to more advanced techniques.
Materials
Segmented wood turnings can be made in many ways. There are three options: ring construction, stave construction or solid non-segmented. Wood expands in a perpendicular direction to the grain. The turner must be aware of the non-parallel grain directions, and take precautions to prevent damage to the piece. This book will provide the foundations and help you explore the different types and styles of wood turning.
Feature Rings
Feature Rings are a special feature on many segmented bowls. The zigzag elements that turn on their sides create an almost lightning-like effect in the ring of the segmented box. The final turning is then sanded down to 600 grit, and coated with clear lacquer. These ring shapes make great gifts or home decor. This DVD is 120 minutes long and shows you how to make segments bowls.
Construction of rings
There are many ways to create rings for segmented wooden turnings. The technique can also be used with solid non-segmented wood. Wood expands in a direction perpendicular to its grain and moisture content. The shape of the ring can be affected by non-parallel grain directions. This must be considered by the turner when designing the segmented turns.
Stave construction
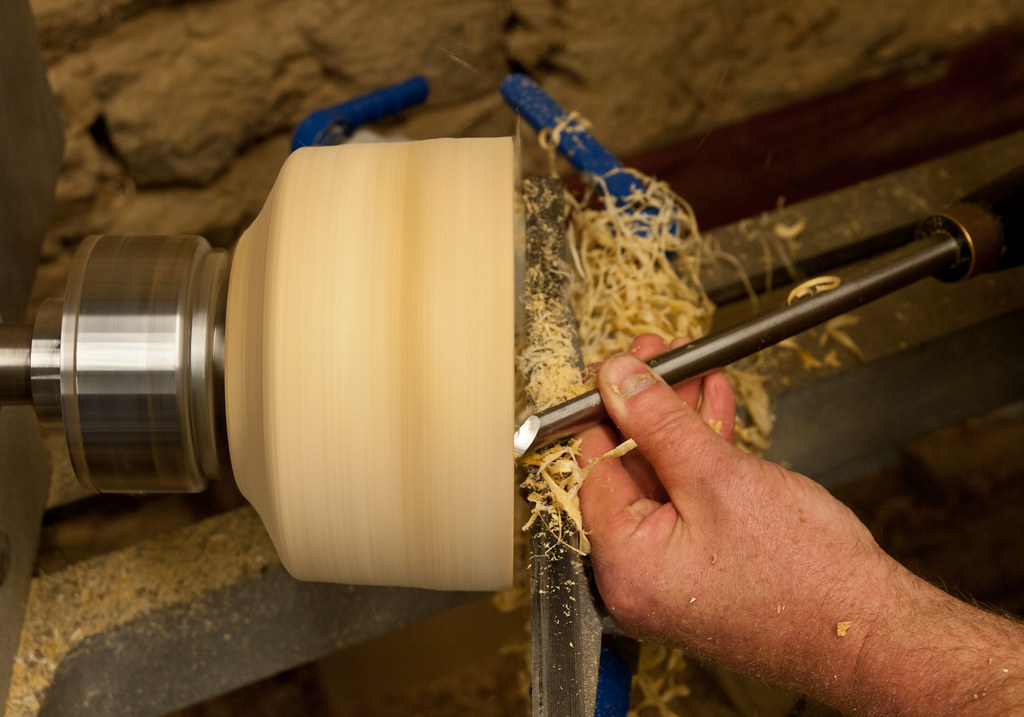
There are two types of segmented wood-turning: the ring and the stave. For some projects, the ring construction is the most popular. However, stave construction can be more prevalent. While both styles have their merits, ring construction is usually easier to achieve and may be more appealing to beginners. This article will discuss the differences between stave and ring construction and how you can apply them to your next segmented job.
Solid wood
It is important to accurately measure miter angles when making solid wood sectioned turnings. Segments can vary in width depending on the size of the ring. When gluing segments together, you must use PVA wood glue with end grain against the grain. Pairs of segments may be glued together at once. These segments can be held together using clamping rings that are fitted with hose clamps. For eight segments, it is recommended to use a miter angle in the range of 22.5 degrees.
Floating base
Avoid using a flat or sloped base when creating segmented wood turns. A floating base can prevent base failure by minimizing stress on the piece. Floating bases can be made from a half-mortise joint where a solid disc fits in the gap, allowing the wood to move freely. Floating bases also have a high level of stability, especially if you use quarter-sawn lumber. A floating base should be no larger than 6 inches in size.
FAQ
What are the basics of woodworking?
It is an excellent way to learn how to build furniture. You can make a simple bench yourself. This project can be done with any kind of wood that you have at home. If you are unsure what type of wood is best, you can get cheap pine boards at Lowes (or Home Depot) instead. After you've constructed your bench you'll want sand all the rough edges off and varnish it.
What should a woodworker be paid per hour?
The hourly rate paid to a professional woodworker is dependent on many factors. These include skill level, availability, and location.
An hourly wage for skilled woodworkers is between $20 and $50.
A woodworker with less experience may be able to charge $10 an hour.
What type of wood should I choose?
Woodworking is a popular job that involves oak, pine and maple. Each type of wood has unique characteristics that affect the look and feel of the final product. Oak is a darker wood and tends to be more durable than other types. Birch is light and soft, while mahogany can be heavier and more dense. You also have the option of solid wood or veneers. Veneers can be described as thin sheets of wood that have been glued together in one layer.
Where can you buy your woodworking materials?
There are many places that you can find all the information you need. You could also visit hardware stores in your area or shop online at Amazon.com.
You can also look for used furniture at flea markets or garage sales.
How do I know what type of wood I'm dealing with?
Always inspect the label when buying wood. The label should provide information about the wood species, moisture content, and whether preservatives have been used.
How can I keep my shop organised?
The first step toward keeping your workshop clean and organized is to set aside a designated area for storing tools. Keep your tools away from dust and debris, so they stay sharp and ready to work. Use pegboard hooks to hang tools and accessories.
Statistics
- If your lumber isn't as dry as you would like when you purchase it (over 22% in Glen Huey's opinion…probably over 10-15% in my opinion), then it's a good idea to let it acclimate to your workshop for a couple of weeks. (woodandshop.com)
- Most woodworkers agree that lumber moisture needs to be under 10% for building furniture. (woodandshop.com)
- In 2014, there were just over 237,000 jobs for all woodworkers, with other wood product manufacturing employing 23 percent; wood kitchen cabinets and countertop manufacturing employing 21 percent. (theartcareerproject.com)
- Average lumber prices rose about 600 percent between April 2020 and May 2021. (familyhandyman.com)
External Links
How To
Tips for driving a nail in wood
First, choose the right size and type of tool to drive a nail through wood. There are many types of hammers that you will find: claw hammers and sledgehammers; mallets; ball peen hammers; and hatchets. Each type has its strengths and weaknesses. For example, a claw hammer works best when you want to hit something hard, like nails; however, it's difficult to control precisely where the blow lands. A sledgehammer is great for hitting large areas at once, but it's too heavy to use effectively for smaller tasks.
Once you have chosen the right hammer for you, put your hand flat against its side so that it rests comfortably in the palm of your hand. Grip the handle firmly, but don't squeeze it so tightly that you hurt yourself. The hammer should be held straight up with your wrist relaxed. You should then swing the hammer straight up, keeping your wrist relaxed. You should feel the impact of your hammer hitting the nail. Try swinging a hammer using a block wood to practice until you are comfortable.
The hammer should be held close to your body when you are ready to begin driving the nail. To ensure that the nail is perpendicular on the surface of the wooden floor, position it. Keep your attention on the tip. Move the hammer forward and then continue to move the hammerhead. You can repeat this several times, increasing your swing speed. Once you've mastered the technique, try adding power to your swings. Try holding the hammer above your shoulder and bring it down forcefully. This will allow you to exert more energy.
Once you've nailed the first hole, remove the hammer from the nail. To pull out the remaining nails, use a screwdriver or pry bar. To avoid splitting the wood, make sure the nail heads are not touching the board's surface.