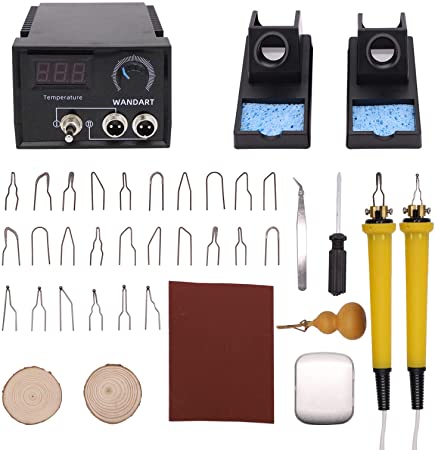
You might be interested in learning about pyrography on Cedar if you are interested in creating unique pieces for your home. This ancient art involves burning intricate designs into wood. The resultant burn marks make beautiful dark designs. This can include landscapes as well as portraits. This method is popular for home decor and has been used for centuries.
Yoko sugi ban
The technique of shou sugiban, which is charring wood's surface, was developed in Japan in the 18th century. This produces a rich charcoal black color to the wood's surface. It can also give it an alligator skin, or crack appearance. Japanese cedar is a popular choice for a rustic, traditional look. Other wood species are possible with varying degrees. The wood's resistance to future damage is strengthened by the controlled charring process, which makes it an ideal preservation technique.
Shau sugi ban
The way char is removed is the main difference between shou suugi ban and traditional sanding. Shau sugi ban woodworkers scrape the charred top layer with wire brushes, while others use coarse sandpaper. Either way, you need to scrape enough char away to reveal the brownish-black color underneath. This will result in an alligator-skin-like effect. You need to sand the excess char.
Shau sugi ban on cedar
The shou sugugi ban of pyrography gives wood a lovely finish. However, this ban has practical implications. Not only can bits of charred wood be tracked throughout a building, but they can also be inhaled by people inside the treated space. Pyrographers have begun to use propane torch instead of traditional wood-burning methods to combat this problem. Here's a comparison of these styles.
Yaki sugi bans basswood
A centuries-old Japanese technique, yakisugi ban on cedar, can add beauty and durability to wood. This process, sometimes called Shou sugi ba, involves charring wood's surface to create beautiful patterns. It is so common in Japan, cedar is used for many shou-sugi ban projects. Satoshi Yamamura, the operations director of a Japanese wooden company, explains why shou Sugi Ban is so popular and what this means for woodworkers.
Yaki sugi bans blue stain pins
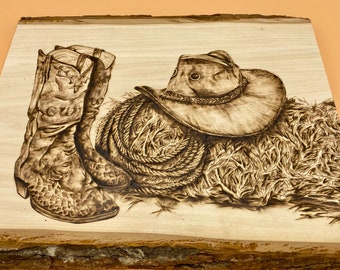
This process, commonly referred to as shou sugi ban, uses fire to preserve wood. Traditionally, cedar is used to perform shousugi ban. But other woods can also be used. Although cedar is a traditional wood for this process, yakisugi can be applied to other types of wood, including maple, ash, or birch. This technique is popular among traditional Japanese craftspeople.
Shau sugi ban on basswood
Charring cedar wood gives it a rich, dark black color with distinctive crackled edges. Cedar is naturally resistant and repels bugs. However, the surface that has been charred can be used to shape wood. The charred wood is available in two types: reclaimed and untreated. To achieve a subtler, burnt look on a cedar panel, you can treat it.
Shau sugi ban on jelutong
Shou sugi ban is a prohibition on pyrography on wooden surfaces. There are many benefits. This technique improves the wood's natural patterns. Because of the thicker carbon layers, charred timber is more durable. This will depend on the type of timber and the environment where it is used. Shou sugi ban is a great option if you are looking for an environmentally-friendly way to treat wood.
FAQ
How can you calculate the woodworking price?
Remember to keep costs as low as you can when calculating project costs. Always make sure you get the best price on materials. You should also consider other factors that could impact the cost of your project, such as experience, skill level, time, and money. If you want to get an idea of what you can expect to spend on different types of woodwork projects, check out our guide to the average price of common household DIY tasks.
How can I tell what kind of wood I am working with?
Always verify the label on wood purchases. The label should detail the wood species, its moisture content and whether it has been treated or not.
What kind of tools are used to carpenters?
Carpenters use a hammer as their most common tool. A hammer is used for pounding nails into wood. They can also use it to hold the pieces together as they work on a project. Other tools include clamps. pliers. screwdrivers. measuring tape. pencils. saws. drills. wrenches.
What kind and type of wood should i use?
The most commonly used woods for woodworking are oak, maple, cherry. Each wood type has its own characteristics which affect the final product's appearance and feel. Oak tends to be harder and darker than other woods. Birch, which is lighter and soft, is more heavy than mahogany. You can also pick between veneers and solid wood. Veneers are thin sheets or wood that are glued together into one layer.
Statistics
- Woodworkers on the lower end of that spectrum, the bottom 10% to be exact, make roughly $24,000 a year, while the top 10% makes $108,000. (zippia.com)
- The U.S. Bureau of Labor Statistics (BLS) estimates that the number of jobs for woodworkers will decline by 4% between 2019 and 2029. (indeed.com)
- Overall employment of woodworkers is projected to grow 8 percent from 2020 to 2030, about as fast as the average for all occupations. (bls.gov)
- In 2014, there were just over 237,000 jobs for all woodworkers, with other wood product manufacturing employing 23 percent; wood kitchen cabinets and countertop manufacturing employing 21 percent. (theartcareerproject.com)
External Links
How To
How to join two pieces of wood together without nails
Many people love woodworking. You can make useful items from wood with your hands, which is both relaxing and fun. However, there are times when you want to join two pieces of wood together without having to use nails. This article will teach you how to do this to keep your woodwork projects looking great.
First, remove any sharp edges from the wood pieces before you join them. Do not leave any sharp corners as they could cause problems down in the future. Once you have done that, you can begin gluing your boards together.
If you are working on hardwood, you should only use glue on one side. If you are using softwoods such pine or cedar, glue should only be applied to one side. Press the boards down until the glue is fully incorporated. Before moving onto the next step, make sure the glue has dried completely.
After you glue your boards together, drill holes at the joints where screws will be inserted. Depending on what type screw you choose, the size of these holes will depend on how big they are. If you are going to use a half-inch wood screw, you will need to drill at least 3/4 inch deep.
After drilling your holes, drive the screws into the board's backside. You should be careful not to touch the board's front surface. This could cause damage. Try to not hit the ends of the screws when driving the screws. This will prevent splitting in the end grain of the wood.
Protect your finished project now. You can seal the furniture pieces or cover the top. Either way, you'll want to use a product that will last for years to come. There are many options: oil-based varnishes; polyurethane; shellac; lacquer.
These products are available at most home improvement stores. Make sure you get the right product for your job. Some finishes are toxic and should not ever be used indoors. Always wear protective gear when handling any of these finishes.