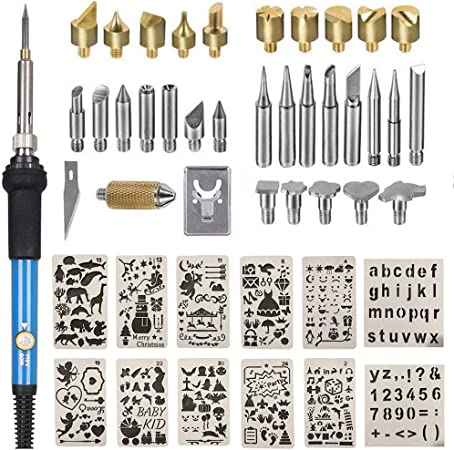
You may be thinking: why do I need a wood burning transfer tip? After all, a transfer tip will be the only thing between you and the surface that you want to burn. You can find a wood burning transfer tip on a variety of products, including a portable stand that can hold it. Before you buy anything, make sure you are familiar with the steps involved in adding a transfer tip to a wood-burning tool.
Carbon paper
Carbon paper can be used as a wood-burning transfer tip. You need to prepare your paper ahead of time. To begin, fold the pattern papers to the back. Next, take a soft-lead pencil and rub the entire design with it. After the transfer is complete, remove the carbon papers and redraw your design. You can also trace your lines with an ink pen. The ink can leave a trace when it burns, so ensure you follow your pattern exactly.
Most buyers agree that carbon paper is easy to use, but some find it challenging to properly use. Many prefer to use trace paper. This works well but it is important to not burn the paper to stop it from tearing. Classic materials are good choices for carbon paper. They can also be reused. You can also save time as well as paper. Carbon paper can also be used for many other purposes. You can usually find the carbon paper in a ziplock bag.
Photo paper
Sometimes you might be tempted just to burn the entire photograph when you burn a photo. To ensure all text is printed correctly, mirror the image. Also, don't touch the glossy side of the photo because it can smear the ink. If you want to transfer a more detailed photo, you can use a chartpak colorless blender pen. This pen costs $5 and is great for transfer of lines and detailed images.
Photo paper is a great choice for transferring designs to a smaller canvas. Photo paper can be found easily and is a great alternative to messy carbon paper. You need to make sure that the photo paper you choose is not absorbs the ink. Lay it ink side down on the wood, and lift it off to reveal a fully transferred image.
Razertip Transfer Shader Pyrography
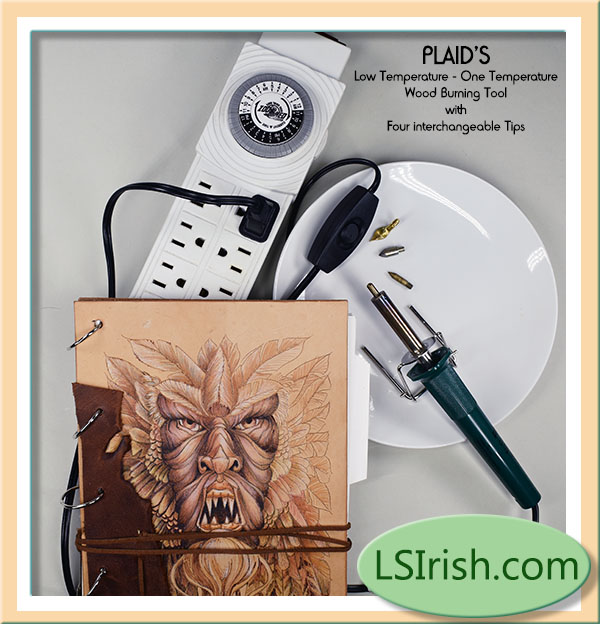
The Razertip Transfer Shader is a popular choice for wood burning tips. The tip is made of stainless steel and has a teardrop-shaped shape. It can be used to shade or transfer heat-photocopied patterns. There are three options for handpieces that can be used to complete a range of projects. Razertip pyrography tools are also available for creating fine lines. For more information, visit razertip.com.
All Razertip pyrography pens come with a one-year warranty. You can choose from hundreds of different tip styles. They are the smallest pens available today, which make them perfect for delicate detail work. They are made to last. The more durable models have thicker tips and connectors posts, larger pen bodies and are more resistant. These models also require a higher heating temperature and a longer cord.
Graphite pencil
A tracing paper is one of the most important things you need when using a graphite tip for wood burning transfer. This paper will help you transfer a design from paper into wood. First, determine the design that you wish to transfer. You have two options depending on the design: a simple one or a more complicated one. Printing the design in advance is an option if you wish to transfer a complicated design.
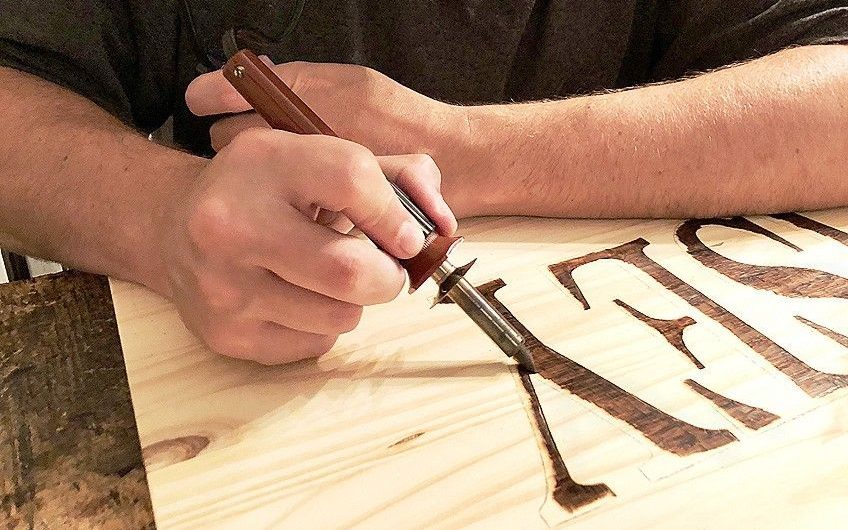
Place the graphite with the dark side facing toward the wood. You can follow the design lines using light to medium pressure. Once you've completed this process, remove the paper. You can now transfer the design. For beginners, you can trace the design directly without needing to use a design paper. However, it won't be nearly as effective as using graphite pencils as it will cause wood to become stiff.
FAQ
How do I know what type of wood I'm dealing with?
Always verify the label on wood purchases. It should have information about the wood species as well its moisture content and whether any preservatives were used.
How can I learn basic woodworking skills
A great way to start learning how to build furniture is by building a simple bench for yourself. This project can be done with any kind of wood that you have at home. If you don't know what kind of wood to use, then go ahead and buy some cheap pine boards from Home Depot or Lowes. After you've built your bench, you'll want to sand off all the rough edges and finish it with a stain or varnish.
Are you able to teach yourself woodworking
You can learn everything best by doing. Woodworking is an art form that requires patience, practice, skill, and experience. To master any craft, it takes time.
It is the best way to learn to do something is to actually do it. So start small and build on what you have learned from there.
What kinds of woods are good for making furniture?
Woods are classified by their hardness. Softwoods can be pine, fir or cedar. They're often used for outdoor furniture because they don't rot easily. The hardwoods include teak, maple, mahogany and oak. They can't withstand the elements outside so they're best kept indoors.
Statistics
- If your lumber isn't as dry as you would like when you purchase it (over 22% in Glen Huey's opinion…probably over 10-15% in my opinion), then it's a good idea to let it acclimate to your workshop for a couple of weeks. (woodandshop.com)
- Average lumber prices rose about 600 percent between April 2020 and May 2021. (familyhandyman.com)
- In 2014, there were just over 237,000 jobs for all woodworkers, with other wood product manufacturing employing 23 percent; wood kitchen cabinets and countertop manufacturing employing 21 percent. (theartcareerproject.com)
- Most woodworkers agree that lumber moisture needs to be under 10% for building furniture. (woodandshop.com)
External Links
How To
How to make wooden joints
This tutorial will show how to join 2 pieces of wood together. We will use the "pockethole joint," which means that we drill holes in the wooden pieces and then glue them together. If your wood has a straight grain, smooth surface, you can use this method. You might consider dowel joinery if your wood isn’t straight or flat. These are the steps
-
Drill Pocket Hole Joints. First, measure the area where you wish to place the pocket joint. Next, drill 3/4 inch holes in each end of each piece using a handheld drilling machine or jigsaw.
-
Sand Smooth. Sanding the wood's edges will ensure that the joint doesn't split.
-
Glue together. Apply glue on both sides of the wooden plank. Allow it to cool for at least 5 minutes before you attach the pieces.
-
Clamp the Pieces Together. After the glue has dried properly, clamp the pieces together to make sure they are flush.
-
Trim Joinery. Trim any excess wood surrounding the joint once the glue has dried completely.
To be able to turn the pieces inside-out, leave enough room between them.