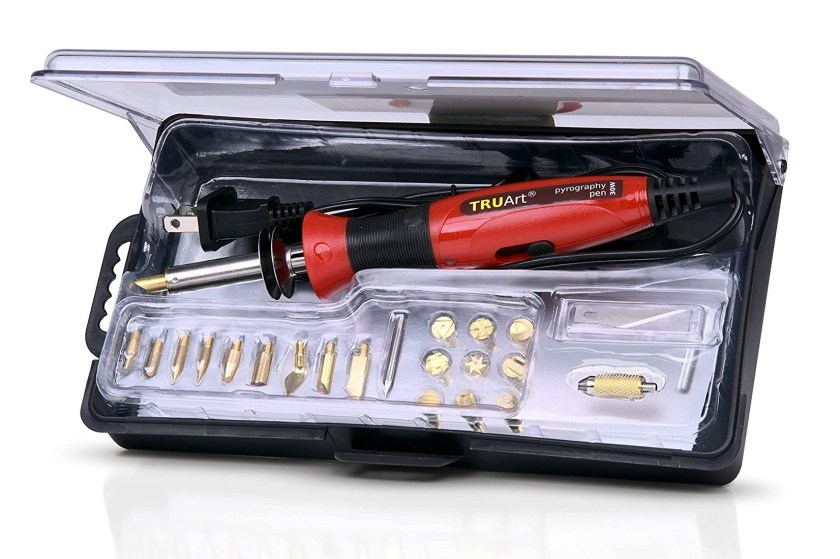
Woodburning is a hobby that you have been studying for a long time. You will probably notice that most articles on the subject are about the latest products. Pyrography (Magazine, Volume 6) is a great example of this. Publisher published this magazine, written by Michael J. Murphy. There are many other magazines you might like to read.
Stuv
Stuv's 30-inch Stuv 30 wood stoves are available in three operating modes: open fire, glass door, and solid door. The stove is easy to see and has a beautiful design. You will be happy with the setting you select, no matter what. You can choose from three different flame patterns, each one bringing a unique characteristic to the overall look of the stove. The Stuv 30 is also more efficient in heat output, providing greater warmth.
Stuv makes woodburning fireplaces. Its modern, square firebox makes it easy to view the fire. It has a frameless, glass door that doesn't obscure your view. The glass can be raised or lowered, depending on your preference. The slim frame makes it possible to use the fireplace either fully closed or with a glass front.
Phelps Pyrography
You can learn more about pyrography by reading the most recent issue of Phelps Pyrography woodburning magazines. Pyrography, a form of wood burning that uses heat for creating designs on a surface, is one example. Although it may appear intimidating at first glance, this art form is one of most rewarding and enjoyable forms of woodburning.
Pyrography simply means writing with fire. The term "pyrography" comes from the Greek words for "pur" or "graphos." This practice dates back to cavemen and was known as fire needle embroidery in the Han Dynasty. Pyrography can be used for both functional and decorative purposes. It allows you to experiment with different materials.
Australian Woodworker
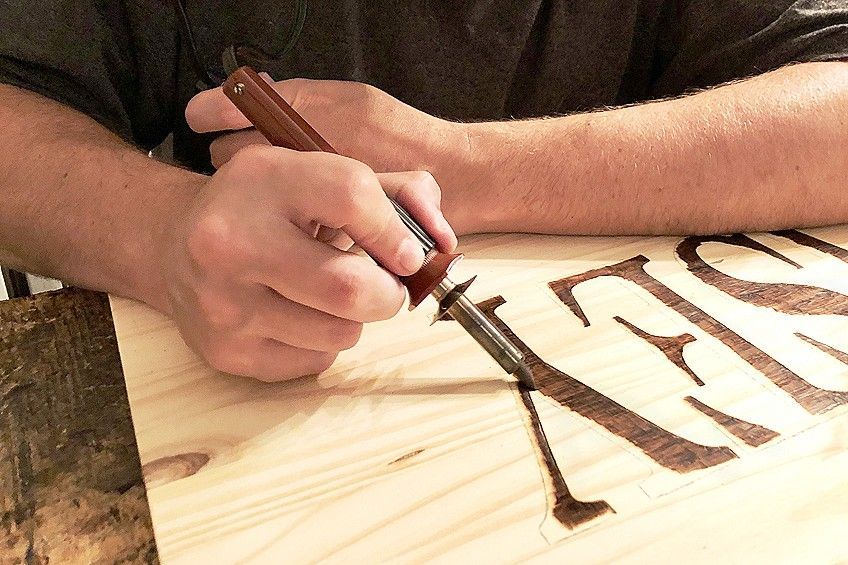
Australian Woodworker, a bi-monthly publication that covers all aspects Australian woodworking, is published twice a year. It is the premier publication for Australian woodworkers. It includes news from the international and national scene as well as the latest techniques. It includes woodcarving by both top professionals and talented amateurs.
Australian Woodworker, in addition to informative articles, features a variety of pyrographers. These include Brian Graham (an Australian Elbowlake artist), David Kreider, Deb Harding, and Francois Peters (a Belgian pyrographer). The magazine contains reviews of tools and techniques as well a comprehensive guide to woodburning. Fox Chapel Publishing is the publisher of the magazine. This company also publishes magazines, books, and patterns.
Mauch's
Mauch had been a drummer for The Ballroom Thieves in Boston a year prior. He tapped into his inner Thoreau and headed out to Maine, where he began to explore pyrography, or burning images into wood. He developed a love for woodburning and published a magazine about it during his trip.
Bowers
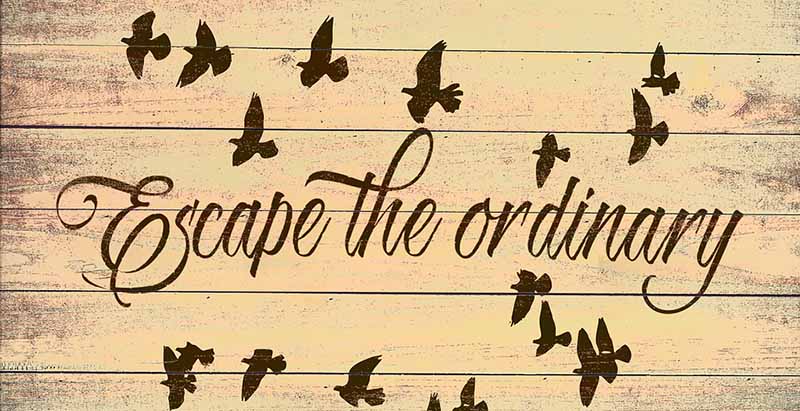
A recent issue of the Bowers woodburning magazine has been devoted to the work of artist Alexandra Bowers. Bowers was born and raised in Scottsdale Arizona. She spent her childhood exploring the desert with her family. This passion fueled her passion. She has sold her work online and at the Made Boutique, downtown Phoenix. Her website also contains information about her art.
Pyrography magazine's Annual Issue is available in stores and on newsstands. It can also be ordered by mail. Every issue includes fascinating articles and creative projects by inspiring artists. The issue also includes reviews of new tools, equipment, and other useful information. Pyrography magazine is produced by Fox Chapel Publishing, which also publishes books, magazines, and patterns. Although most articles are about woodworking and sewing, the magazine also features woodworking and sewing.
FAQ
How often should I purchase new supplies?
Some tools will need to be replaced over time. Hand tools will need to be sharpened regularly. If you are using power tools, you will need to purchase replacement parts regularly. Try spreading your purchases over a few months so you don't buy too many at once.
Do you have the skills to learn woodworking?
Doing is the best way to learn any subject. Woodworking is an intricate art form that requires practice, skill, patience, and experience. Any craft requires patience to master.
To actually learn something is the best way. Start small and use what you learn.
How long does it take for furniture to be finished?
It depends on the type and complexity of your design as well as the amount of finishing that you use. Hardwoods are more difficult to maintain than softwoods. Hardwoods can also be more costly than softwoods. But they last longer, and resist moisture better. It takes between one and three months to finish a piece.
How much money will I need to get started?
Because every project is unique, there aren't exact numbers. These are the factors that will give you an idea of how much you'll need.
-
Cost of materials
-
Tools and equipment
-
Time spent on the Project
-
Your hourly rate
-
What profit are you expecting to earn?
-
No matter if you are looking to hire someone
It's a good idea for beginners to start with small projects like frames and boxes. As you gain experience, you'll be able to tackle more complex projects.
How much should a hobbyist invest to get started?
A lot of capital is required to purchase the necessary supplies and tools if you want to start your own woodworking shop. It's a good idea to buy a small tablesaw, drill press and circular saw. These items aren't very expensive, so you won't break the bank.
How can my shop be organized?
To keep your workshop tidy and organized, you should first create a place for tools storage. You want your tools to stay clean and free from debris and dust. Hang tools and accessories using pegboard hooks.
Statistics
- If your lumber isn't as dry as you would like when you purchase it (over 22% in Glen Huey's opinion…probably over 10-15% in my opinion), then it's a good idea to let it acclimate to your workshop for a couple of weeks. (woodandshop.com)
- The U.S. Bureau of Labor Statistics (BLS) estimates that the number of jobs for woodworkers will decline by 4% between 2019 and 2029. (indeed.com)
- Average lumber prices rose about 600 percent between April 2020 and May 2021. (familyhandyman.com)
- Woodworkers on the lower end of that spectrum, the bottom 10% to be exact, make roughly $24,000 a year, while the top 10% makes $108,000. (zippia.com)
External Links
How To
How to drive a nail through wood
The first step in driving a nail into wood is to choose the correct size and type of hammer. Claw hammers include mallets, claw hammers (sledgehammers), mallets, ball-peen hammers, hatchets, and mallets. Each kind of hammer has its own advantages and disadvantages. A claw hammer works well when you're trying to hit nails with a heavy hammer. However it is difficult to precisely control where the blow hits. A sledgehammer is great for hitting large areas at once, but it's too heavy to use effectively for smaller tasks.
Place your hand flat on the side of your chosen hammer so that the handle rests in your palm. Grip the handle firmly, but don't squeeze it so tightly that you hurt yourself. Hold the hammer straight up, keeping your wrist relaxed. You should then swing the hammer straight up, keeping your wrist relaxed. The impact of the hammer hitting the nail should be felt. Try swinging a hammer using a block wood to practice until you are comfortable.
Hold the hammer near your body until you're ready for the nail to be driven. Position the nail, so it's perpendicular to the surface of the wood. Keep your eyes on the tip. Swing the hammer forward, then follow through with the motion of the hammerhead. You can repeat this several times, increasing your swing speed. Once you have mastered this technique, increase the power of your swings. Hold the hammer high above your shoulders and pull it down. This will allow you to exert more energy.
After you have nailed the hole, take the hammer off the nail. The rest of the nails can be pulled out using a screwdriver, pry bar, or a hammer. To avoid splitting the wood, make sure the nail heads are not touching the board's surface.